The Workshop Press Company UK offers the UK manufacturing market the best and most comprehensive lineup of Hydraulic Metal Presses along with Metalworking and Metal Fabrication machinery. One of our most popular machines is a Profile Bending Machine, but of all Metal Fabrication Machines on the market, this category of bending machine has the most diverse group of names than any other machine and the names include: l
- Profile Bender
- Profile Bending Machine
- Profile Roller
- Angle Roller
- Section Roll
- Section Rolling Machine
- Section Bending Machine
- Section Bender
- Ring Roller
- Ring Bender
- Roll Bender
- Ring Roll Bender
………and may others. All of these names highlight the versatility and functionality of these machines in bending various profiles and shapes.
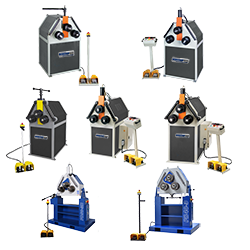
This is a comprehensive overview of Profile Bending Machines, specifically focusing on ring rollers or profile benders. These machines are commonly used in manufacturing and fabrication facilities to bend various profiles, such as bars, tubes, and sections, into rings, circles, or curved shapes. The applications of profile bending machines are widespread and diverse, including industries like construction, art, automotive, marine, and transportation.
The information highlights a wide variety important factors to consider when selecting a profile bending machine. These factors include:
- Manual or Hydraulic Machine: Refers to the method used to position and control the bending roll or shaft. Manual machines typically use a corkscrew mechanism, while hydraulic machines use hydraulic mechanisms controlled by buttons.
- Shaft Size: The size of the shafts, typically indicated by the outer diameter, is an essential parameter used to identify different models of profile bending machines.
- Number of Shafts: Most ring rollers have three shafts, although some models may have four or more shafts for specific applications.
- Movable Rolls and Direction: The movable rolls, also known as movable shafts, determine the bending force and can move vertically or horizontally. The configuration can vary, with either the top or bottom rolls being movable.
- Driven Rolls: Profile bending machines generally have two or three driven rolls that propel the material through the bending process. In most cases, the bottom rolls are the driven rolls.
- Motor Size: The motor(s) of the machine, either for manual or hydraulic operation, should be appropriately sized and designed for the intended bending tasks.
- Bending Roll Positioning Mechanism: Refers to how the bending roll or rolls are positioned and controlled, which can depend on the manual or hydraulic nature of the machine and the number of movable shafts.
- Position Display: The position of the bending roll(s) can be displayed manually with a scale, a digital readout (DRO), or on a computer numerical control (CNC) display.
- Control: Profile benders can be fully manual, hydraulic with digital displays, or equipped with NC or CNC systems. Various combinations of control systems are available.
- Distance Between Shafts: The distance between the centre points of the bottom shafts determines the tightness of the bent ring. The top shaft may also be considered in specific situations.
- Usable Length of Shafts: The usable length of the shafts affects the maximum thickness of rolls that can be mounted on the shafts.
- Standard Section Tooling Configuration: Profile bending machines often come with a set of section rolls, which can bend standard square, rectangle, and round profiles without requiring custom tooling. The configuration of the rolls enables versatility in bending different profiles.
- Base Framework and Materials: The construction of the machine’s base framework can vary, ranging from tubular frameworks with steel plates to more robust structures designed for demanding applications.
- Working Planes: Ring rollers can operate in two planes: one with horizontal shafts and a vertical frontal surface, and the other with vertical shafts and a horizontal frontal surface. The latter position is suitable for long profiles.
Standard Bending Rolls / Bespoke Bending Rolls
One of the most important aspects to consider when investing in a profile bending machine is the adaptability of the machine to various types of profiles. While these machines come equipped with standard “section rolls” that are configurable and well-suited for square and rectangular profiles, there are instances where specialized applications require a more tailored approach.
Section Bending Machines for metal profiles come complete with a set of standard section rolls that are designed to handle common profiles like squares and rectangles. These rolls are configurable, allowing for a wide range of bending operations within standard parameters.
When bending profiles, it is always good practice to fully encompass the profile as best you can, and when doing special profiles, the standard rolls will make this difficult. For those special projects where the standard section rolls are not appropriate, bespoke rolls are available to meet your specific needs. These custom-designed rolls are engineered to suit unique profiles and applications, ensuring that you achieve the precise bend you require, regardless of the complexity of the profile.
The availability of both standard and bespoke rolls adds another layer of versatility to profile bending machines, making them an invaluable asset for any metal fabrication operation. Whether you’re working with common profiles or need a custom solution, the machine can be adapted to meet your specific requirements.
What is the Minimum Bending Diameter I Can Achieve?
The Section Modulus of a Profile Determines the Minimum Bending Diameter
The section modulus (ZZ) is a geometric property of the cross-sectional area of a profile that plays a pivotal role in determining its bending capabilities. By understanding the technical nuances of section modulus, one can achieve a level of mastery over profile bending operations, ensuring that each bend is both structurally sound and aesthetically pleasing.
Manufacturer Guidelines
To assist the metal fabricating engineer and help them circumvent a wide variety of calculations and geometrical laws, manufacturers produce charts that specify the bending capacities for different profiles using the properties of mild steel as the baseline. This eliminates the need for operators to perform complex calculations.
Precision vs Trial and Error
While profile bending machines can be highly precise, many operators revert to trial and error to determine capacities. The approach can either be technical, relying on calculations and manufacturer guidelines, or empirical, based on hands-on experience. Either way, profile bending machines require the metal bending engineer to be hands-on and switched-on.
Considering these factors in conjunction with each other is crucial when selecting a profile bending machine that suits specific requirements and production facilities.
WorkshopPress.co.uk otherwise known as The Workshop Press Company is a company specializing in selling profile benders. If you need more specific guidance or assistance contact us directly at 0800 999 1090 or info@workshoppress.co.uk and one of our professional staff will be happy to assist you.