Deep Drawing Presses
The RHTC hydraulic deep drawing presses have large table sizes and accelerated speeds providing excellent production performance.
This hydraulic presses series comes with a main upper cylinder and a hydraulic cushion integrated into the lower bolster of the pressing machine. When carrying out a deep drawing process, the two hydraulic cylinders meet to start the metal forming operation. The implemented forming die set dictates the shape of the resulting pressing. This forming process is widely-used in many different industries, two of them being the Automotive and Medical Industries.
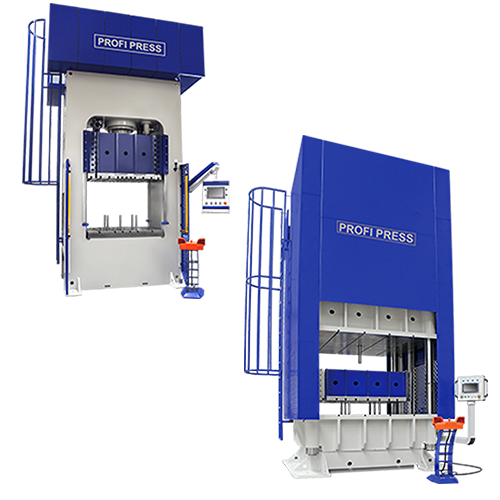

UK Expertise
1-3 Days Delivery
USA Sales
Nationwide Service
Ireland Sales
Fast Delivery to Ireland
Worldwide
Global ShippingWhat is Deep Draw Pressing?
Deep Drawing Pressing Explained
The pressing process call Deep Drawing is a manufacturing process used throughout the world to form sheet metal into desired shapes and creates such items as pots, pans, metal storage containers, automobile panels, gas tanks, panels for white goods, and many more. The terminology “deep drawing” seems self-explanatory but from a technical manufacturing perspective this process refers to a press component that where its overall depth from top to bottom is the same dimension or greater than the diameter of the press component.
Deep Drawing uses flat metal pieces that can be individual sheet metal pieces or the pressing process uses a coil of metal that sits on a coil feeding machine and is then run straightening device as the metal is fed into the press. Components can be formed in one stroke or they can be formed progressively as they move through the press and die setup. Generally speaking, when creating pressed products, the more complex the geometry and contours of the item becomes, the more difficult it is to product that item with deep drawing and pressing operations.
The tools that are used for press forming and deep drawing are generically called the punch and die, and are attached to die sets so that they can be securely attached to the top slide plate and bottom bolster plate of the hydraulic deep drawing press. The top die component is referred to as the punch and contains the shape form of the item to be pressed, and then the bottom die component is called the die and is the negative image of the punch and must be a proportionately larger than the punch in order to allow for the thickness of the material to be shaped by the two components. Punches and dies are designed to accept a particular sheet metal type and thickness, or a range of thicknesses can sometimes also be successfully used. The punch and die are more often than not made from a high quality tool steel but contingent on the particular application plastics and carbides are know to be used also.
As stated above, the Sheet Metal that is used to make the press components is either sheet metal blanks or is taken from a coil feeding mechanism and is positioned and secured over the die opening, and once in the correct location the pressing cycle is then activated and the punch proceeds downward into the die correspondingly forming the metal. The forming process, depending on the item being formed, can be shaped in one cycle, or more complex items may need to be formed in a progression of pressing cycles.
With deep draw pressing, as with any pressing process, there are a variety of factors to consider, and material type and thickness are often the first two factors discussed in conversation relating to press forming operations. The shape, geometry, and related radii of edges and corners of the pressed component is another major factor that needs to be considered and then will correspondingly relate to how much shearing force is required to form the press component.
Deep Drawing Presses come in a wide variety of configurations and can be of powered by a mechanical or hydraulic mechanism and come in a variety of framework configurations and tonnages. The size of the framework, the pressing mechanism, press controls, and the weight of the machine itself are all considerations when choosing the correct press for your applications. Required production units is another consideration, but in general deep drawn parts can be formed at a rate from 100 mm to 300 mm per second. Deep Draw Stamping is a practical solution for many applications and offers many benefits to a manufacturing facility wanting to produce complex geometrical parts with the minimum press cycle time as possible while reducing the require labour per unit, thus reducing costs and increasing profitability.
A variety of industries use deep drawing process including Aerospace, Automotive, Energy, Defense, MoD, Shipbuilding, Switching Cabinetry, Whitegoods, Medical Devices, Oil and Gas, Rail, and many other industries.