Press Brakes
TALK TO A SPECIALIST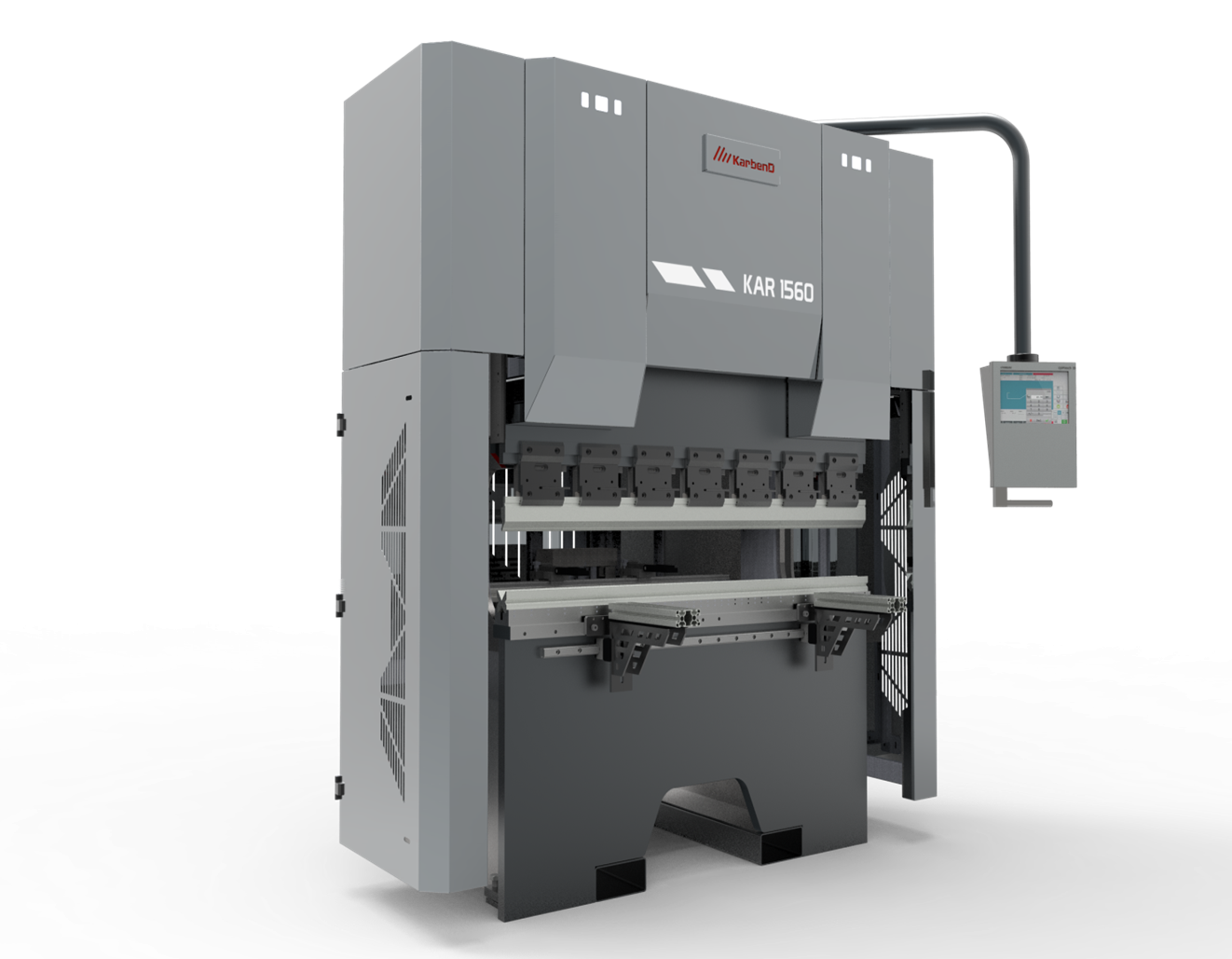

UK Expertise
1-3 Days Delivery
USA Sales
Nationwide Service
Ireland Sales
Fast Delivery to Ireland
Worldwide
Global ShippingWhy is a “Press Brake” called a “Press Brake”?
The term “Press Brake” has had a long-winded evolution and the name flounders many people, but “Brake” has evolved over a few hundred years from a variety of similar words throughout various regions of the world, and quite simply means “to bend”.
A Press Brake is a type of metalworking press or metal fabrication machinery that is designed to bend sheet or flat plate metals, and its overall general framework resembles the framework of a standard metal forming punch press, but from end to end is typically longer and front to back typically narrower. The operating components of a standard power press are modified to create a press brake. For example, the top slide plate of a traditional power press is replaced by a elongated RAM or BEAM that has a clamping mechanism to allow bending tools or punches to be attached to it. The bottom bolster table of a traditional metal forming press is replace by an elongated BED that has a mounting system on it that allows for dies to be securely attached to it. The typical T-Slots that you would find on the slide and bolster of a standard power press are replace with clamping and mounting systems. The bed remains static and the BEAM moves up and down in a vertical path and lowers the punch down onto the die, and when the punch engages the metal the up and down motion bends the flat metal to the desired pre-set bend angle.
There are a large variety of variables to consider when determining what Press Brake is right for your application and they include, the material type to be bent, material thickness, the length of the bend, the radius of the bend, and production run quantity.
Press brakes range from very simple to being quite complex, and some of the features that need to be considered are what tonnage you need to bend your typical applications. Typically overcompensating this figure provides leeway in the workshop from a capacity standpoint, but can require a larger upfront investment. The length of the press is another consideration, and press brakes will typically come in widths starting at around 1 meter and go up to several meters long. Typical production run quantity is another factor to consider. If you typically do long run production change over time is not as big of a factor as when you are doing many small jobs in a short period of time. If you do many short run jobs investing in a more advanced tool clamping system such as a quick release systems will reduce changover times. Other consideration will be if you should invest in a Manual Crowning or CNC Controlled Crowning system, Automated Backgauge, Sliding Supports, and modified Safety Systems.
What types of press brakes are there?
Going back in history all presses were powered by a flywheel and clutch mechanism, but things have progressed and typically all press brakes are hydraulic, electronic servo, or a combination of the two, and the description of the press brake will more often than not include such designations. For example “hydraulic press brake”, or “electric servo press brake”. Typically hydraulic presses deliver large tonnage while the electric servo type machines operate quicker and are used for lighter gauge materials.
Press Brakes are used in a wide variety of industries. Some common press brake applications are: Automotive panels, Airframes, Metal artwork, Furniture, White goods, Metal containers, Ship building, Rail, Steam Gas Turbines, and Renewable Energy.