Notchers for Tube & Pipe
Tube notchers are an essential bit of equipment especially in a workshop were handrails, roll cages, and tubular structures are manufactured. A high-quality tube notcher can save a business time and money and at the same time improve the quality of products produced.
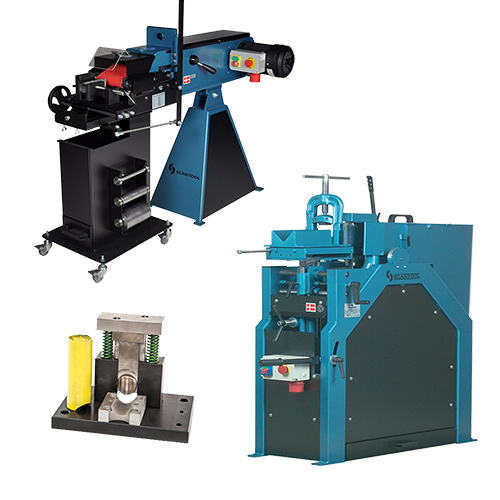

UK Expertise
1-3 Days Delivery
USA Sales
Nationwide Service
Ireland Sales
Fast Delivery to Ireland
Worldwide
Global ShippingTube notching is the process of taking part of the end of the two bold so that it nicely mates up to another tube either in a straight-on on 90 degree angle forming a T-Joint or other such angles as 45 degrees or 60 degrees. The typical outside diameter for tubes being notched is between 25 mm and 60 mm with wall thickness is between 1 mm and 5 mm. Larger tubes and pipes can be notched with the right tools and equipment. Common materials are mild steel, stainless steel, copper, chromoly and titanium.
Some common applications for tube notching are handrailing, roll cages, motorcycle frames, bicycle frames, artwork, street furniture, manifolds, marine railings and ladders, and a variety of other applications.
The notching process is carried out in a variety of fashions one very common and economical process is with a whole cutting tool on the end of an electric drill. another way of carrying out tube notching is with an roughing end mill within a milling machine or on the end of a motorised shaft. Third way of notching is using a press tool where the tube is slid over the end of the tool and the press descends an notch’s out a piece of the tube. a fourth way of two notching is with an abrasive belt on a power belt grinder. Each process has its drawbacks and benefits including cost, accuracy, ease, noise, mess, and efficiency.
Tube notching with a hole saw is an economical process because all you need is an electric drill and a support structure such as a vice, and you are on your way. Most workshops already have an electric drill in a hole saw on hand. This makes notching with a hole saw a very popular way of going about tube but it is not very efficient, it is not very accurate, and you can go through a lot of holesaws in a short time, putting the economy of the process to the test.
The pressing operation can be very efficient and economical but you must either invest in a press and a tool or have a press then you can put the tool into already. This process is fast and can be very accurate but there is a downfall and that is that you are limited to what angles, tube diameters, and wall thicknesses you can notch. A press-style notching tool is typically specifically designed for a particular tube outside diameter, wall thickness, and notching angle. If you are consistently doing straight-on 90 degree notches to for a T-Joint this can be a very efficient process but one thing that must be considered is that you only notch one side of the tube per one stroke and the tube must be rotated 180 degrees to do the second notch which can lead into an accuracy issue if the operator is not attentive. This process can be a very economical to set up and run contingent on the quantity of tubes you need to notch.
The roughing end mill process, depending upon the setup, can be highly accurate but you need some serious equipment to carry out this process. A formidable vertical mill and vice are required or a machine with highly accurate and sturdy rails and a motor driven shaft would be another way of going about it. These machines typically are not cheap and the roughing in mills can also be pricey in addition.
Tube notching with a belt grinder is a very efficient, accurate, and cost-effective way of notching tubes and pipes of all types, diameters, wall thicknesses, and materials. When properly configured the process can be very clean and noise can be reduced to a minimum. This process is carried out with an industrial belt grinder and an industrial sanding belt along with varying sized roller mandrels that the tube is pushed on to the bearing roller to notch out the end of the tube to the appropriate size to allow it to mate up to another tube neatly in a tidy fashion. The process starts with the operator setting the notching angle of the vice. There is a angle scale that works in coordination with the vice that helps the operator accurately set the notching angle. Once the tube is mounted into the vice the machine is started, and the operator moves the vice forward with a lever device on to the notching mandrel and rotating sanding belt. The typical cycle time of this process is between three and five seconds. When the machine is outfitted with the proper exhaust equipment dust is collected in a neat and tidy fashion. Tube notchers based off of belt grinding machines is reasonably cost effective but super duty and highly accurate belt grinder tube notching machines are also available. These machines are meant to do tube notching each and every day all day long. The life of the belt is contingent on what materials are being used and the operator, but with the appropriate belt the operation in carry on for many notches before change-over is required.
The Workshop Press Company sells European built Scantool Belt Grinder based Tube Notching machines as well as Press Based notching tools. Please talk to one of our representatives to help you determine what machine or tool is appropriate for your particular application. We can be contacted on our e-mail at info@workshoppress.co.uk or at 0800 999 1090.