Elevate your workshop’s capability with the 300 Ton Heavy-Duty Workshop Press. Engineered for reliability, it offers a blend of power, precision, and customization to meet the specific needs of your projects. Features include a fully motorized operation, NC control for precision, and adjustable table plates, making it ideal for heavy-duty pressing tasks.
Technical specifications for Standard 300 Ton WSP
- Pressure force [kN]: 2943
- Maximum pressure [bar]: 260
- Piston stroke [mm]: 480
- Oil delivery [ltr/min]: 12/33
- Oil capacity [dm³]: 100
- Working speed [mm/sec]: 1.80
- Approaching speed [mm/sec]: 4.90
- Return speed [mm/sec]: 6.20
- Motor power [kW]: 5.5
- Voltage [V]: 400/3
- Frequency [Hz]: 50/60
- Revolutions per minute [rpm]: 2800
- Insulation protection [IP]: 54
- Working width [mm]: 1750
- Weight [kg]: 3150
Features
- Movable cylinder (left-right)
- Dual acting cylinder
- Integrated pressure manometer
- Pressure regulation
- Hydraulic unit with two speeds
- In height adjustable working table
- Joystick for the control of the piston
- Hand pump for precise press work
- 2 year warranty
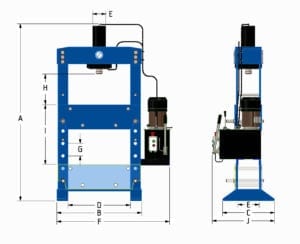
Dimensions for Standard 300 Ton WSP
- A: 2250
- B: 2120
- C: 985
- D: 1750
- E: 500
- F: 2550
- G: 177
- H: 180
- I: 531
- J: 1085
- K: 420
Diameters
- Inside diameter of cylinder [mm]: 380
- Diameter of piston rod [mm]: 180
- Diameter of piston head [mm]: 215
Customisations & Modifcations
- 1-Phase Motor
- 60 Hz Motor
- Bespoke dimensions
- System Inetegrations
- Bespoke Applications
Optional Accessories & Tools
- V-Block sets
- foot pedals
- hand controls
- additional safety features
- system integrations
- mandrel sets
- corner rounding notchers
- corner wedge-shaped punches
- corner notchers
- hole punches of all shapes and sizes
- tube and pipe notching
- drain hole nibbler punch
- brake press tooling
- custom tools
Motorised Workshop Press Chart
Technical Features
- 300-ton pressing capacity
- Motorized hydraulic operation for ease of use
- NC control for precision pressing tasks
- Customizable table plates to fit specific project needs
- Robust construction for durability and longevity
- High-pressure hydraulic system for consistent performance
- Safety features including emergency stop and guard shields
- Easy to operate controls for efficient workflow
- Adjustable pressure settings to suit various materials
- Energy-efficient design reduces operational costs
Product Uses
- Metal forming and shaping
- Assembly and disassembly of large components
- Straightening of plates and shafts
- Pressing bearings, gears, and bushings
- Molding and laminating applications
- R&D testing for material strength
- Repair and maintenance of heavy machinery
- Fabrication of custom parts and tools
- Compressing materials for density testing
- Punching and cutting metal sheets
Technical Features
- 300-ton pressing capacity
- Motorized hydraulic operation for ease of use
- NC control for precision pressing tasks
- Customizable table plates to fit specific project needs
- Robust construction for durability and longevity
- High-pressure hydraulic system for consistent performance
- Safety features including emergency stop and guard shields
- Easy to operate controls for efficient workflow
- Adjustable pressure settings to suit various materials
- Energy-efficient design reduces operational costs
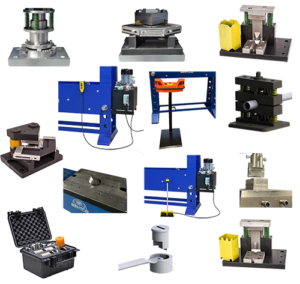
View the Press Accessories Category
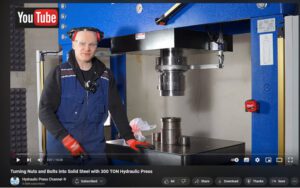
In a captivating video by the well-known Hydraulic Press Channel, they showcase the incredible power of a special 300-ton press by compressing various nuts and bolts into a single billet. This demonstration of extreme pressure highlights just one of the press’s many applications. Similar uses include metal shaping, part consolidation, material testing, and creating composite materials from disparate pieces, offering a glimpse into the press’s versatility and potential for innovation in material science and engineering. For more details, check out their video on YouTube or contact us.
The Workshop Press Company UK
Phone: 0800 999 1090
info@workshoppress.co.uk
Product Uses
- Metal forming and shaping
- Assembly and disassembly of large components
- Straightening of plates and shafts
- Pressing bearings, gears, and bushings
- Molding and laminating applications
- R&D testing for material strength
- Repair and maintenance of heavy machinery
- Fabrication of custom parts and tools
- Compressing materials for density testing
- Punching and cutting metal sheets
Optimize your operations with our 300 Ton Heavy-Duty Workshop Press, a pinnacle of RHTC hydraulic technology designed to enhance profitability and expand capabilities in your workshop. This premium press supports a broad spectrum of applications, including bending, folding, straightening, and more, providing unmatched durability, reliability, and efficiency to save time and costs while maximizing productivity.